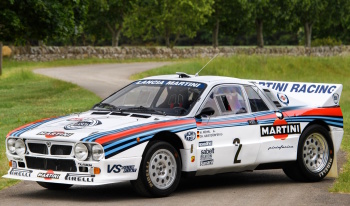
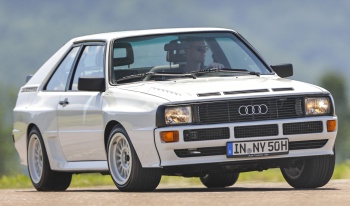
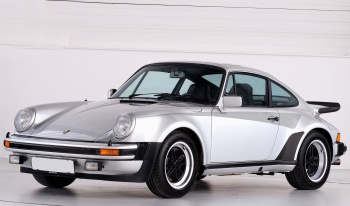
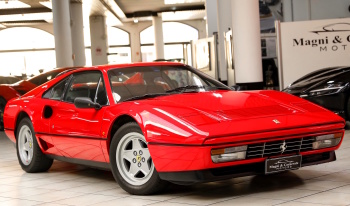
You'd only find turbochargers on high-end sportscars, supercars and race/rally cars in the 1970s and the 1980s. Today, turbos are everywhere, even on small family hatchbacks
Due to increasingly stringent emissions norms and the need for improved fuel efficiency, one option that car manufacturers are increasingly going in for is engine downsizing. Smaller engine capacity, fewer cylinders – that’s the formula for reduced emissions and better fuel economy. However, to ensure that smaller engines are still able to deliver the kind of power and performance that customers expect, manufacturers often use forced induction – turbocharging, supercharging or, in rare cases, even both.
Once the exclusive preserve of high-performance sports cars and supercars, forced induction engines are now commonly used across many vehicle segments, including smaller sedans and hatchbacks. In India, while turbocharged diesel engines have already seen widespread use over the last 10-15 years, a few turbocharged petrol engines have also been introduced in recent years, not just by high-end luxury car manufacturers but also by more mainstream carmakers like Maruti, Volkswagen, Skoda, Kia, Renault/Nissan, Hyundai and others. Increasingly stringent emissions norms necessitate the replacement of bigger, naturally aspirated engines with smaller, turbocharged units that not only deliver the required horsepower, but are also more fuel efficient. The advantages are manifold – fewer, smaller cylinders in a forced-induction engine means reduced internal friction levels, and better torque output even at lower engine rpm. And yes, it’s important for new engines to deliver strong low-rpm torque, since high engine revs often means bigger valve overlap (between intake and exhaust valve operation), which often means increased emissions.Naturally aspirated engines can have a brake mean effective pressure (BMEP) of anywhere between 80 to 200psi, while turbocharged engines start at around 220psi, going up all the way to 320psi, with the potential being there for even higher pressure. Hence, with better volumetric efficiency and higher specific output (the ratio between an engine’s size vis-à-vis its power and torque output), smaller forced induction engines will inevitably continue to replace bigger naturally aspirated engines.
Turbocharging vs Supercharging
Both turbochargers and superchargers are simply different types of forced induction technologies and adopt slightly different ways of achieving the same objectives. Both are used to pressurise the intake tract, thereby achieving better combustion and volumetric efficiency. Turbos use the vehicle’s exhaust gases to spin its blades and are usually mounted very close to the engine’s cylinder head, which is why they can also run quite hot, requiring an intercooler to keep temperatures within reasonable limits. Bigger turbochargers also exhibit some turbo ‘lag,’ since there is noticeable time lag between the driver pushing the accelerator pedal, the engine revving up, the exhaust gases spinning the turbocharger’s impeller and then, finally, the engine coming ‘on boost.’ To avoid this, some manufacturers, especially with their higher-performance sports cars, use two smaller turbo units rather than one big turbo, since the smaller units can spool up at a faster pace.
Superchargers, which are most often used on petrol engines and very rarely on diesels, are operated via a pulley and belt, which in turn runs off the engine’s crankshaft. They produce a more constant pressure curve, do not have the ‘lag’ that’s often associated with turbochargers and can achieve better low-rpm drivability as compared to turbochargers. Superchargers can be centrifugal, Roots-type or screw-type. Centrifugal superchargers are driven by a belt that runs off the engine and are usually good for maximising high-rpm power. Roots-type superchargers are essentially large air pumps that pull air in, compress it and pump it into the engine’s cylinders. With these, compressed air flow to the engine is usually not as consistent as it is with centrifugal superchargers, though the torque curve can be more linear, making it a good option for low-rpm power and improved drivability.
While Roots-type superchargers compress the inlet charge within the engine’s cylinders, screw-type superchargers use a set of internal rotors to draw in and compress air within the supercharger unit itself. Screw-type superchargers can be relatively more expensive as compared to other supercharger types and are often found on higher-end cars. Regardless of the type, though, superchargers allow variable levels of boost pressure, which can be altered by changing the pulley size and making the supercharger spin at higher speeds. More boost means more power, of course, though levels must be contained in accordance with engine compression and the engine internals’ capacity to tolerate very high levels of heat and pressure. Excess boost can cause what’s called ‘detonation,’ which is the spontaneous combustion of leftover air/fuel mixture in the engine, which causes great harm.
Advances in Forced Induction Tech
Turbocharging first came to F1 in the late-1970s, and by the mid-1980s, some F1 cars’ turbocharged engines were producing as much as 1,000-1,400bhp. So, yes, turbocharging is certainly a very effective method of boosting an engine’s power output. Early turbos weren’t all that effective in street use, given their very high operating temperature and the dreaded turbo lag, which affected drivability. However, with continued development and refinement, turbochargers have now evolved far beyond the capabilities of their 1980s predecessors. Currently, for cars sold around the world, more than 50% are already fitted with a turbocharged engine, and that figure is as high as 75% for European markets.
Modern turbochargers are made of titanium and aluminium alloys, which means reduced weight – the blades can spin up much faster, thereby reducing lag. To reduce internal friction, manufacturers have also started using ball bearing cartridges and oil-free air bearings instead of older journal and thrust bearings, for improved efficiency. Additionally, new blade configurations and compressor wheel designs are also helping manufacturers improve the way a turbo works. Apart from improvements in materials and design, there’s also changes in the way the turbo unit is employed. Multi-stage turbocharging, for example, where two turbos are used instead of just one – a smaller unit, which spins up faster at lower speeds and helps eliminate low-rpm lag, and a bigger unit for increased overall boost levels.
High-performance engines demand that turbochargers run increasingly high pressure, and one solution that’s now being implemented in this context is the use of variable geometry / variable vane turbos. These are currently quite complex and expensive and are only being used on very high-end cars, but can provide a big increase in performance. With variable vane turbos, ‘vanes’ in the turbine housing can be made to open up or close as needed. At lower rpm, the vanes remain partially closed and becoming ‘tighter,’ allowing the turbo to spin faster. At higher revs, the vanes are opened up more, allowing some of the exhaust gases to stream past, negating the need for a wastegate to bleed excess pressure.
The other challenge is dealing with heat, which can go up to 1,000 degrees Celsius for some turbo units. Currently, air-to-air and air-to-liquid intercoolers are used to cool the intake charge after it leaves the compressor. Newer technologies like water-injection and inter-stage cooling are also being used. With the latter, an intercooler is fitted between two series turbos, which lowers the temperature of the primary turbo’s compressed air output before it enters the second turbo, thereby improving power and efficiency. With water injection, a fine mist of water is constantly sprayed on to the turbo unit at very high pressure to cool it down. Furthermore, some newer turbos also use a water-cooled compressor housing, which keeps temperatures down and helps increase engine performance and efficiency.
Electric Assistance
Once heat is taken care of, manufacturers start thinking of ways by which they can increase the pace at which the turbo spools up, and one of the newer methods – employed first by Volvo in its ‘PowerPulse’ system – is the use of compressed air to boost turbo performance. Using a pressurised air tank and an electrical compressor, the system uses a valve that opens up under heavy throttle application, feeding fresh pressurised air to the turbo and delivering immediate response.
Manufacturers are also looking to take this one step further in the future, by using an electric motor-generator to increase turbo performance. Such an electric motor can spin the turbo at very high rpm without using exhaust gases, thereby eliminating lag entirely. Such electrically-assisted turbochargers can use the energy from exhaust gases travelling at high speeds, to generate electricity, which in turn can be stored in a supercapacitor that can route that energy to power a hybrid’s electric motor. While the possibilities are endless, such e-assisted turbocharging systems are currently unproved for street use and would require 48V electrics to run – not possible with a lot of current production cars.
Most of the above, in terms of developing electric assistance systems for the blower, is also relevant for superchargers, which aren’t as popular as turbos but are still being used by many carmakers, especially on high-end sportscars. As with turbos, the aim with electrically assisted superchargers is to achieve the ability to generate rapidly variable boost pressure, without relying on changes in engine speed for the same. Electro-mechanical actuators that can achieve this are already in production, offer full integration with modern engine management systems and negate the requirement for a wastegate.
Electric superchargers, their manufacturers claim, also result in a setup that’s more cost-effective, more emissions friendly and less complex in terms of thermal management. With the development and inevitable move to 48V electrics, electrically operated superchargers are likely to find their way on to mainstream production cars in the foreseeable future.
Future Directions
The old automotive adage that says ‘there’s no replacement for displacement’ will soon no longer hold true. Also, some manufacturers will go down the route of ‘if one is good, two must be better.’ I’m referring to the use of both turbocharging and supercharging in one engine, something that’s already been happening for the last three decades, and which might become more popular in the future.
Volvo’s ‘twincharged’ T6 engine, for example, uses a turbocharger as well as a Roots-type supercharger for more linear, robust power delivery across the entire rev-range. The advantage of this setup is that the supercharger, which is more efficient at low and mid rpm, takes care of boosting power and improving low-rpm response, while the turbo takes care of top-end performance. In the Volvo engine, the ECU operates a valve at around 3,500 rpm, which then declutches and bypasses the supercharger and allows the turbo to take over. This setup provides best possible power, drivability and fuel economy for any given engine displacement, though possibly at the cost of added cost and complexity.
As for the future, the direction is very clear – given new emissions norms and the need for engines to provide improved power and torque at relatively lower rpm, and the advantages that turbochargers and superchargers offer in that context, the normally aspirated engine’s days might just be numbered.
I wrote this article for Auto Tech Review, when I was working as the magazine’s executive editor in 2016-17. Due to some difficult circumstances, ATR had to be shut down a few years ago.
No comments:
Post a Comment